Using a torque wrench with a crowfoot wrench (also known as a crow wrench) is handy when you need to torque fasteners in tight or recessed spots where a socket won’t fit. But there’s a small trick to it—you need to adjust the torque setting because the crowfoot extends the lever arm of the wrench, affecting accuracy.
Â
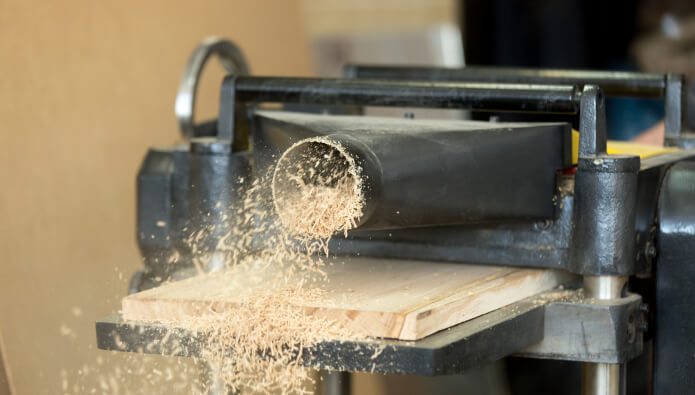
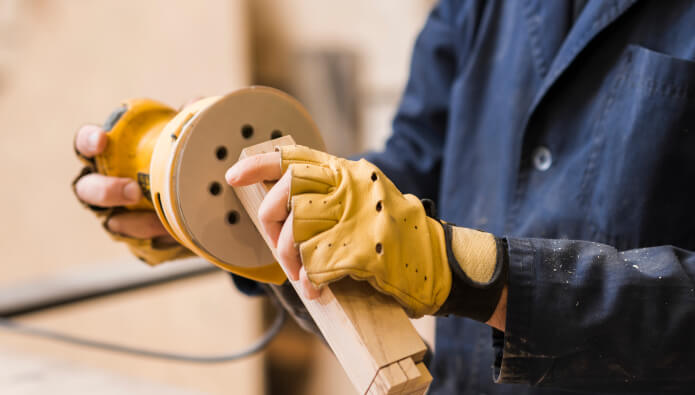
Currently as of 2021, an electric motor is the most popular choice to power stationary tools, though in the past they were powered by windmills, water wheels, and steam. Some museums and hobbyists still maintain and operate stationary tools powered by these older power sources. Portable electric tools may be either corded or battery-powered. Compressed air is the customary power source for nailers and paint sprayers.
Formula Inputs
T1 – Torque specification for the fastener.
L – Effective length of the torque wrench. Measure from the center of the square drive tang to the indicator line on the handle of your Tekton torque wrench. First, set the torque wrench to the torque spec for the fastener (T1) and then measure in a straight line parallel to the body of the wrench. Most Tekton micrometer torque wrenches have a groove in the knurled handle grip. Tekton split beam torque wrenches have a line in the center of the handle. (For other brands of torque wrenches, check the manufacturer recommendations, or use the center of the handle grip if the manufacturer does not recommend a location).
C – Change in length caused by the crowfoot wrench. Measure from the center of the fastener to the center of the square drive tang on the torque wrench. Measure in a line parallel to the body of the wrench. If the position of the crowfoot wrench decreases the effective length of the torque wrench, creating a negative change, then input this amount into the equation as a negative number.
Formula Output
T2 – Final torque wrench setting that you should use. This will correct for any change in leverage caused by using the crowfoot wrench.
Add comment